|
Resume
I start and finish projects; that's what I do best.
I've been involved in a very diverse range of experiences. Not just as
a casual observer, but as an active contributor. Everything in this
world relates to everything else, and a breadth of experience is highly
valuable. I have composed this portfolio together to illustrate the
depth to which I have been involved in all these areas. I never want to
misrepresent my experience, but I want to avoid the mistake of
downplaying the reality of what I have accomplished.
This portfolio represents my past. The
future I am working toward is outlined in my Space Management Roadmap. My hopes are to be among the prime players in the growing
Commercial Manned Space Exploration Industry.
US Patent: Rock Climbing Port-a-ledge
|
|
We
can start off with the patent I filed in October '04 for a
port-a-ledge
for sleeping on rock climbing routes requiring multiple days to climb.
It’s a good eye catcher, and it illustrates experience in mathematical
analysis, manufacturing, ingenuity, intellectual property, and the
ability to start a project and see it through to completion.
The attached article (Ledge
Development.doc) was submitted and selected as one of the winners
of the
Collegiate Entrepreneurs Organization and NCIIA Technology Competition (Technology
Awards; p. 4). It
illustrates the development process and business prospects for the
ledge. It is significant that I designed and built this ledge on my
own, everything from machining all the joints to sewing the bed and
suspension cords.
The attached structural analysis is pretty straightforward (Structural
Analysis.doc). This analysis is for the dual climber model of the
ledge, not the single model shown here (right). I don’t recall what
grade I earned in my structures class, but I do recall how to apply
what I learned.
It was clear that I didn’t want to build a business around this single
product, so it would be best to patent it, and license it to an
established company. I did some personal research on patent law, then
happened to find a class I could take on intellectual property. After
the class, I decided to draft the application on my own, for the
learning experience, and then hire a professional to complete the
process, to ensure it was done right. Simply put, I have a functional
understanding of the legal and business implications of intellectual
property, and how aspects of intellectual property effect industry.
You can find more on the ledge if you visit the web site I built to use
for marketing it to the established climbing companies. www.speedledge.com.
(You must use MS Internet Explorer for the speedledge site to work
properly)
|

Zion Canyon; Utah -
Moonlight 5.10/C2
|
Return
to Top |
|
|
Satellite Test Chamber Control System
Northrop Grumman |
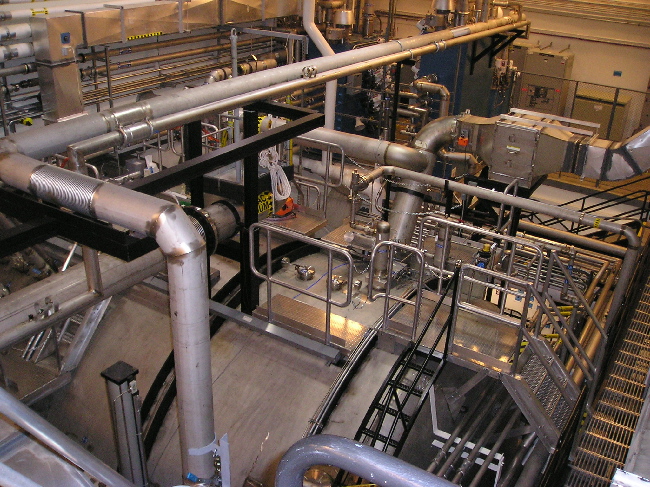
We control everything back here... |
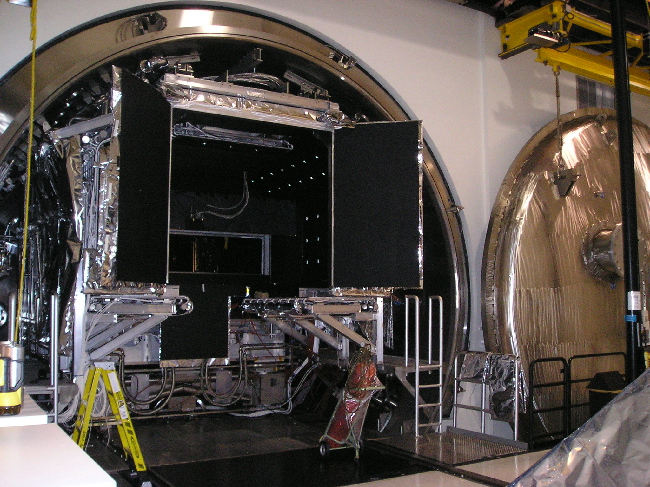
... to simulate space in here.
|
Satellite Test Chamber Control System
This project required programming all the software to monitor, command,
and
log data for the entire vacuum chamber test system, as well as
integrating new equipment. This chamber is
26 ’Diameter, by 40’ deep, with over a thousand sensors, valves, pumps,
and
components. The programming involves 12 different sets of software, all
running on 6 independent (but interacting) process controllers,
requiring nearly 4000 tags in the whole system, with 5 local and remote
user interfaces. The initial challenge was learning the system, with
all the components and their interaction. Once I understood the
existing setup, then I could move into designing / redesigning for our
needs.
The original control system for this
thermal-vac test
chamber was hastily implemented, and consequently had several recurring
bugs. I expressed my interest in the project with the intent to improve
the reliability, streamline the processes, implement a reliable and
accessible database, and add several user friendly bells and whistles.
When I started this project, I set forth an expected schedule of 14
months to completion, with mile markers every 3 months or so.
My manager thought the schedule looked good, but when our
lead facility engineer saw it, he laughed: “Ok. Multiply that by 3 and
that
might be your schedule.... You work quickly though. You might get it in
2 years.” I met each of my mile markers along the way, and completed
the project exactly 1 month early,
March 31, 2005!!! The end result is a control
system superior to what we
initially envisioned, no bugs or glitches (after two week long tests),
and a database that users can easily and intuitively access.
The early finish wasn't an accidental slip of circumstance. Our
facility schedule changed
and I had to accommodate. We wanted to run a baseline test at the end
of
March, and that included our Control System. We saw this coming in
December, so I spent the next three months working overtime, and the
last two weeks on an 80 hr schedule. If I finished in time for this
baseline, we could have the project completed. If I missed the
deadline,
it would drag out for another couple months. My manager was
understanding if I couldn't make it, but I wanted it finished, so I
put in the work and got it done.
Technical aspect:
I used LabView for the
primary user interface, and LabView DSC for the database and tag
engine. The process controllers are Allen Bradley SLC/505 series,
programmed in RSLogix 500 (ladder logic). Local user interfaces for the
process controllers are Allen Bradley PanelView touch screens. Other
equipment interfaces through LabView on GPIB and RS 232.
System Control Interface (LabView) - Built from scratch
System Database with User Access Interface (LabView DSC) - Built from
scratch
Thermal
System ladder logic (RSLogix) - Major changes
Thermal System local interface (PanelView) - Built from scratch
Vacuum System ladder logic (RSLogix) - Minor changes
Vacuum System local interface (PanelView) - Minor changes
Vacuum Gauge communication (LabView - GPIB) - Built with LabView
Electronic Equipment Chillers
(LabView - RS232) - Modification and Integration
Nitrogen Thermal Control Units (RSLogix and PanelView) - Led a summer
intern to make changes
Data Analysis tools (VBA in Excel) - Led a summer intern to program
from scratch
|
LabView -
Vacuum System Overview screen.
|
LabView
back panel (code) segment for the charting routine.
|
Return
to Top |
Hired
Minds: A Guide for Graduating
Engineers
|
|
I have written Hired Minds to serve
as a transition guide for graduating engineers, and am currently
working on publication. The idea for this book came from the
Engineering Resume Workshops
noted below. The book uses the personal
experiences of over two dozen beginning engineers to illustrate the
several paths for developing engineering experience as an undergrad,
landing the job you want, and starting off right as an engineer. It
covers the office, team, and personal work dynamics that are essential
to successful engineering, especially during the first year. The book
is designed to accompany University senior design project courses,
helping to successfully bridge the transition from education to
industry.
I first completed writing Hired
Minds on July
11, 2005, at 3 pm. Following that, I had the manuscript reviewed
by several relatively new engineers. The next round of reviews came
from several senior managers, including my Site Director at Northrop
Grumman, our head of Employment and Recruiting for nearly thirty sites,
and a Program Manager at Boeing. When
published, the work will be just under 200 pages.
I had never written a book before,
but
the process and
organization came rather intuitively. However,
I must say
that in order to write something like this, you have to be in the right
frame of mind, and you need dedicated segments of time to lock out the
world and focus. Overall, it has been a very valuable experience.
|
*I'll post the cover here
when it's ready.
|
Return
to Top |
|
Visual Basic Data Analysis
Northrop Grumman
|
|
When I started with Northrop
Grumman, I was hopeful to build my
experience in the direction of automation, particularly regarding the
mechanical / software interface between hardware and programming. I had
enjoyed my previous experience in this area, and it was an interesting
area to enter.
The first assignment I was given at NG was to chart eight months worth
of temperature data from previous thermal-vac tests. While showing me
the data format and what knowledge they wanted to gain from the data,
my manager commented “It would be nice to have a macro where we could
just push a button, and have all this done for us.” I replied “I might
be able to do that.”
I had never so much as opened the Visual Basic Editor in Excel, but I
had heard from a few people in the past that Excel could be programmed
to manipulate data like this. I spent the next week and a half with the
help menu, books borrowed from co-workers, and Google, developing a
macro that processed and charted all the temperature data just like we
wanted it. The data that they expected would take me a week could now
be processed in three minutes.
About two months later, we had a bank of heaters in the vacuum chamber
fail during test. During the next 48 hours, the engineers who knew the
chamber and it systems were over there trying to determine if the
payload was safe, what happened, etc. When it was all done, Brent (my
mentor) found me to say “That macro you wrote saved us hours, and
hours, of crunching data to find out what happened. Could you make
another macro that would…” And so began the automation of the routine
data analysis for two test chambers, and our radiometric calibration
data. 9 Tools total, including one for our Payload Thermal Analysis
team.
With all of the macros I have
written, I have done
everything I can to make them robust, and very user friendly. I have
programmed each macro for other non-Excel people to use it.
I put together a workshop for young
engineers, and posted samples that you can download from my web site (VBA for
Engineering Applications).
|
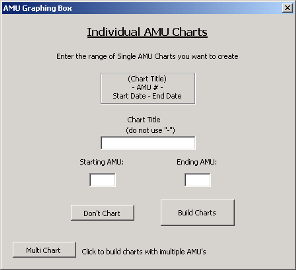
Dialog Box from the RGA
Macro.
|
Return
to Top |
|
Engineering Student Workshops
|
|
While
at NG, I have had the opportunity to participate in recruiting
new engineers from universities, interviewing candidates of various
experience levels, and working with the summer intern program. On my
first recruiting trip with NG I interviewed over 30 engineers, and
noticed that many students had more valuable experience than what they
represented on their resume. A couple months later, while talking with
a friend who was graduating soon, I caught the idea of running an Engineering
Resume Workshop for the students prior to the next career
fair. In two weeks I contacted the appropriate professors at BYU, put
together the presentation, and flew out to run the workshop. It turned
out to be a tremendous success with over 60 engineers showing up, and I
was working with individual engineers on their resumes from 6 pm until
midnight. I also helped several through email who couldn’t stay that
late.
Toward the end of that semester, I was making a trip to Utah to climb a
multi-day wall with my brother, and decided I would take the
opportunity to also teach a mini-course on VBA in
Excel for Engineering Applications. The course notes are available
on my web site, along with several demonstration macros. Over the next
few months, I received emails from a few engineers who applied what
they had learned through the workshop.
I have run resume workshops at BYU each semester, as well as a workshop
through AIAA for students in various universities in the Los Angeles
area. Each of these experiences have been highly valuable for the
participating students, as well as myself, in gaining exposure to so
much diversity in engineering talent, experience, and background.
It is significant to note that these workshops were not previously
offered. I saw the need to be filled, organized the workshops on my
own, and contacted the faculty to get approval to hold these workshops.
|
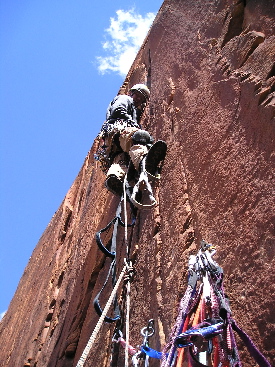
Zion Canyon; UT - Space
Shot C2
No relevance to the workshops, except that it's from the climbing trip
mentioned.
|
Return
to Top |
|
|
Aerospace - Government
Washington DC Visit - AIAA
Through regular attendance of AIAA meetings and events, I meet many
people diversely involved with various aspects of the Aerospace
Industry. I was invited to join a group from AIAA to meet with several
Senators and Representatives in Washington DC. This trip was far more
valuable than I had anticipated. We made our each visit in small teams
with different people each time. The various reasons each individual
had for supporting the same AIAA agenda was very enlightening. The
government side of the discussion was the most eye opening. The
Senators and Representatives (and their staff) have so many issues that
they are responsible for dealing with that they need individuals
concerned about their industry to schedule times to discuss their
industry and opinions about what should be done. If individuals do not
take the time to communicate with our elected representatives, they
will have a relatively limited basis of information and rationale to
formulate their decisions. One of the most valuable discussions I took
part in was at a cocktail party at the end of the day. Our elected
representatives have taken the responsibility to make decisions for
legislating and funding programs, but the citizens have an equal
responsibility to work with these public officials.
In a nutshell, there is a whole dimension of Aerospace I had previously
been only vaguely aware of. I include this experience in this portfolio
because I am aware of how valuable it is to a rounded understanding of
the industry. Engineering is the core of aerospace, but as providers of
technology for our national defense, there are several other aspects
that are indispensable to success.
|
Return
to Top |
|
SpaceHub.org - www.spacehub.org

When I decided that commercial space exploration was the direction I
wanted to take my career, I immediately began investigating the
industry. The societies and membership groups are always advertising
themselves, but I was interested in the businesses and technologies
that would make commercial space a reality. I wanted to know where it
would be most effective for me to personally focus my talents within
the
greater effort being made. I began collecting my own research on the
industry, and then spoke with a friend at work about posting the
research as a web site where we could generate collaborative input
from the worldwide space community. A short time later, I spent two
solid days with a friend in the web programming world building the
framework for the site, and it has grown from there. Having the
research as a web site has proven valuable for myself, as well as the
increasing visitors to the site.
We have a long-term vision regarding what we would like to use
SpaceHub.org for. Ultimately, we would like to use the site as a design
forum for the engineering necessary for a sustained human presence in
space. Modeled after the astounding success of the Open Source
community in programming, we would like to draw from the worldwide
talent pool in engineering. There are many
significant challenges to this, but we believe the idea may have merit
when we have the right tools. There are many
differences between programming software and designing spacecraft, but
who would have thought Open Source could achieve what they have
already? It's a possibility. Capitalism and individual ambition are an
astounding combination.
|
Return
to Top |
|
X Prize Volunteer Crew Manager
August - October 2004
Mike Melville on SpaceShip One after the
first civilian
flight into space; June 21, 2004.
The X Prize was a $10 Million competition
for the first privately funded team to successfully launch a vehicle
with the equivalent of three human passengers into sub-orbital space,
and repeat the trip within two weeks. When I heard there was going to
be a test launch for Burt Rutan's SpaceShip One, I gathered some
friends and went out to Mojave for the event. While there, I met the
team responsible
for running the X Prize, discovered they needed help with the upcoming
launches for the
$10 million prize, and was more than happy to join up with them.
I immediately started meeting with the X Prize team to prepare for the
competition launches that would be held in the next few months. Because
of my familiarity with the airport, comfort with working with groups of
people, and reliability with a few initial projects,
they asked me to co-train and co-manage the entire
volunteer team for the competition launches (over 150 volunteers).
I prepared the training presentations, and worked with the sub-team
leaders to organize our efforts. During the event I co-managed the
volunteer crews, ensuring
they had the resources and support they needed. Everything went through
smoothly, the launches were an event for
the history books, and we were happy to be a part of it all.
*On a personal note, the first launch on June 21st, 2004, was a very
influential event in my life. Several years earlier, I had dismissed
the notion of space travel because I wasn't interested in sparring
against other people to hitch a ride on the Space Shuttle. Furthermore,
I strongly believe that indiviuals should earn their means to go play /
explore in space. Seeing SpaceShip One successfully developed under
private funding, at 2% to 5% of the cost of a single shuttle launch,
validating a legitimate business market, I realized that a frontier I
thought to be closed was actually within reach. I want to walk on the
Moon, after 100 people have been there before me. I want to earn my way
there, and ensure the industry infrastructure is present to accomplish
this. This is the motivation behind my Space Management
Roadmap.
|
Return
to Top |
|
El Capitan; Yosemite - Tallest Cliff in
North America
August 2004
|
Morning on day 6, pitch 32, about 3,000 ft from the base.
Greg Gardner on belay, now in Medical School at St Louis.
|
|
5 1/2 days living on the face of a 3,200 ft vertical rock.
It took us
ten years, and three attempts to reach this goal. We started like any
other rat-headed high school kids learning to climb. Top-roping, sport
climbing, trad climbing, big walls (overnight), and then El Cap. We had
our dream of climbing El Cap, and kept tackling bigger and tougher
routes. Sometimes we'd learn from a successful climb, and sometimes
we'd learn from getting ourselves out of trouble. We learned how to
judge the extent and limits of our abilities, how to rely on each
others strengths as a team, where we could push the envelope, and when
it was time to back off.
The unexpected difficulty in a climb this large is the mental and
psychological demands. Every minute of the day you are consciously
aware of every component in your entire system, continually
anticipating your moves as a team, and staying prepared for whatever
may happen. You finish the day with a mental fatigue rivaling the worst
projects and exams from college.
It really is difficult to describe the feeling of looking up the next
pitch, the sun beating down on you, knowing it's going to be tiring,
difficult, you may take a couple falls, and this is the pitch that
commits you to finishing the rest of the route. You and your brother
are the only two who can get you off the rock, and the only way
to get there is up. You experience what it means to commit to finishing
what
you start.
You don't make it up a wall by following the standard "recipe for
success." There aren't any coaches, teachers, grades, or degrees
encouraging you to take on the goal. You do it because it's going to
take everything you got, a diverse range of ability individually and as
a team, an extended period of commitment... and
your personal belief that you can pull it off. Life doesn't arrange
itself for you to
walk to success, you have to work every step of the way, earning your
way there.
|
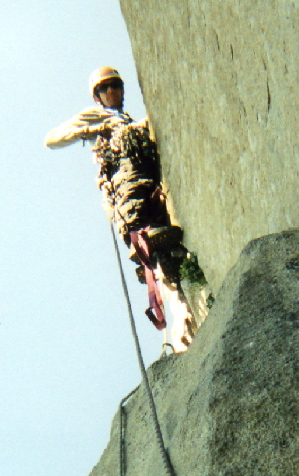
|
|
Return
to Top |
|
Project Manager - Dual Shuttle Vacuum
Forming Machine
(Sorry, no
pictures right now)
This eight month project was more like a pre-graduation full time
contract than an internship. Quality Plastics wanted to increase their
vacuum forming capacity, and wanted to implement some features into
their machine that they could not buy from the regular suppliers (such
as distortion graphics and pressure forming). The machine had been
modeled in CAD (IDEAS) when I arrived. I was responsible to bring the
machine from computer screen to reality in 8 months.
This machine is a plastics vacuum forming machine with two forming
stations on opposite sides of a shared infrared heating station. It has
a forming capacity of 4’ x 5’ sheets, and the entire machine is 18’
long, 10’ wide, and 9’ tall. The work pieces are clamped pneumatically,
carried by stepper motors, and the forming platens are hydraulically
actuated. Because the company also wanted to use this machine for
pressure forming and distortion graphics, it was essential that the
machine be
very rigid with high positional repeatability.
The first thing I did upon arrival was to study and become familiar
with the machine, its intended uses, and what had driven the design
decisions. Next I laid out a schedule covering all the tasks that
needed to be performed to complete the machine, starting generally and
branching down to the detailed components (based on a GANT Chart
format). Before beginning to order materials, I composed a budget
including all the known and estimated expenses. Finally I began
ordering materials and executing the fabrication and construction.
Through all the machining, welding, etc, it was very interesting to see
first hand how different materials react to different manufacturing
processes. Gaining exposure to the various materials, coatings, and
processes that enhance material properties opened my eyes to a whole
range of possibilities to manipulate component performance. To make
some specific components, I took advantage of the expansion ratio
between steel and aluminum in building the tooling. I used metals of
different hardness, damping, and bearing properties for function
specific components (bronze, brass, “gray iron,” UHMW polyethylene,
etc.).
I thoroughly enjoyed managing this project and driving the progress
every day on it. As the project started gaining momentum, I was given
more
people to work for me. For two months at the peak of the project, I had
5 others working under my direction, some skilled and some requiring
training. All the fabrication
decisions and many detailed design decisions still had to be
generated as we went. Designing all this fast enough to keep my workers
busy led to six weeks in a row of working between 65 and 75 hour weeks.
Making that machine grow so quickly during that time was certainly
worth the focus and dedication, and I still made time to go mountain
biking 2 – 3 times a week.
|
Return
to Top |
|
Asphalt Zipper - Senior Design Project; BYU
|
Stress analysis generated using Cosmos on the model created
in SolidWorks
|
|
No fancy write-up yet, just pictures. But... our team of five designed
EVERYTHING for this machine, the company's shop built it, we tested it,
and it met or exceeded our performance specifications. It was a good
Capstone project for our degree.
.
|
Return
to Top |
|
Automated Dice Drill
I programmed two of these. The first was a 14 Axis machine with two
drilling stations, and the second used only one drilling station with a
proprietary feedback mechanism. I programmed the second as a side
project while I was working on the Dual Shuttle Vacuum Forming Machine.
Both machines drilled repeatably within position and depth tolerances
of +/- 0.002”. We used servo motors controlling the axis, and brushless
servo motors for the drills because of their high torque and small
size.
|
In the view shown, the cubes are fed in through a cartridge
(starting at right), clamped into an anvil by a pneumatic cylinder,
carried into the drill station where three servo controlled drills were
coordinated to simultaneously drill the necessary holes. Then the cube
was ejected through a transfer chute (left) and properly oriented for
the second station (not shown) to drill the remaining three sides.
|
|
The real challenge was in optimizing the process, and at the same time
making it idiot proof. The program was run through a PC interface
(Think-n-Do Software) communicating with the servo drivers and I/O
units controlling the pneumatics. There were many commands that had
initially been programmed to unnecessarily wait for previous operations
to finish. There were many more commands that could be triggered
inadvertently, resulting in crashing the machine. The challenge was in
finding which operations it was necessary to wait for, how long to wait
for them, how to flag commands prior to their natural sequence, and to
insert the necessary interlocks that would prevent these processes from
beginning impulsively while allowing them to begin when desired. In
total, I brought the cycle time from 12 seconds down to 5 seconds, and
worked out (apparently) every program bug.
It is significant to note that when I was hired as an intern, it was
never the company's intention to give me responsibility over this
machine. Among my other responsibilities, I was helping their full time
engineer develop the program and build the smaller mechanisms to finish
the mechanical functions of the machine. More often than not, I was the
one left to dig through and analyze the maze code, to understand the
problems we were running into. Over time, I became the expert on the
machine, and they gave me full responsibility for it.
When we finally delivered the machine (on time) to the company we had
contracted to build it for, everything went perfectly. The President of
Quality Plastics planned on me delivering the machine and spending the
day before he came setting it up. He arrived expecting to stay for
three days trouble shooting the inevitable problems that would appear.
When he arrived, he saw I had everything under control and gladly flew
out the next morning, confident that I could handle anything that came
up, and leaving me to train the new owners and operators.
|
Return
to Top |
Composite Human Powered Vehicle
|
|
Composites
have always been fascinating. The best part of this
experience is that everybody who was on the team was there simply
because they wanted to have a good time, and we'd learned enough
engineering to do it. We gained exposure to composites in both pre-preg
and wet lay-up, auto-clave curing, and the functional performance of
the materials (we broke a couple parts) The body and frame had been
designed by a pervious year senior design team, so we didn't get much
on that aspect. We saw how composite materials can be fabricated to
produce very specific and directional performance. They’re not a
cure-all design material, but can be very useful in the proper
applications.
My friend and I started this team. He had the idea and we both picked
it up and ran. He took care of all the logistics and paperwork for the
team, and I got to take the role of the Chief Engineer (partly due to
circumstance, and my previous experience in a machine shop and with
composites). The rest of the team was a mix of friends and random
recruits conveniently interested in exactly what we needed people to
take responsibility for.
|
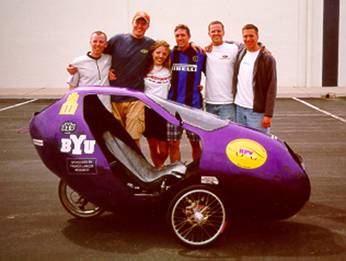
HPV Team and vehicle after
winning first in the Utility Race at the ASME national competition in
Reno, NV.
|
Return
to Top |
|
Investment Banking
|
|
In
January ’02, nearly a year before graduating in Engineering, I
discovered investment banking, and spent that entire year doing
everything in my power to take my career toward Corporate Finance, or
Mergers and Acquisitions.
In addition to my engineering courses, I took classes in Accounting and
Corporate Finance. One of my projects was an investment analysis of
Sylvan Learning including all the historical financials and
projections, and other dirty work to become familiar with the industry.
To become more familiar with the industry, I wrote a term paper on The Rise and Fall of Enron for my
Technical Writing class (document re-formatted). After grading it, my
professor suggested that I consider writing for the Wall Street Journal
as a career. Not my type of job, but I was flattered. I spent about an
hour every day reading the WSJ, focusing in the finance section. I also
read several books, including the history of Goldman Sachs, Liars
Poker, and Charles Schwab.
I began networking with investment bankers in New York, as well as San
Francisco, Los Angeles, Salt Lake, and Denver. I spoke with people in
all aspects of the industry from traders, to analysts, to I Bankers,
covering both bulge bracket and mid-market firms. In August I took a
trip to New York to meet many of the people I had spoken with on the
phone, and to interview with a couple of the bulge bracket firms. That
fall I was told by two separate individuals, one interviewing and the
other networking, “You know more about this industry than 90% of the
people I’ve spoken with.”
I tried to make it to Wall Street, but in the end I failed. The Dot
Bomb of ’01 had something to do with that. I'm glad I failed, but I'm
glad I tried. My experience in that industry has been very valuable in
understanding the Aerospace Industry, both with the large and smaller
corporations.
On a side note...
It's funny, the
average GPA for undergrads finishing the Business
School was 3.6, the highest at BYU. The average for undergrads
finishing Engineering was 3.4 (my GPA), the lowest at BYU. The Business
classes I took were easier than any engineering class I ever
took... and they were famed to be the toughest in the business
school!!!
Business students feared these easy classes!!! Where's the Justice?
|
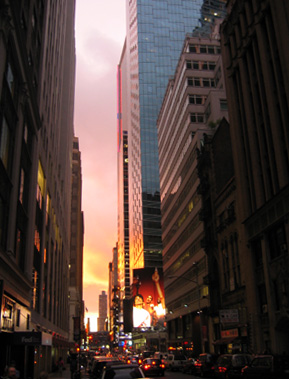
.
|
Return
to Top |
|
|
Manufacturing Emphasis
I did an emphasis in Manufacturing along with my degree in Mechanical
Engineering. I started at BYU in Manufacturing Engineering, but
switched to Mechanical because it opened more opportunity for the
future. Early on, an Uncle and cousin who were engineers inspired me to
develop an appreciation for the manufacturing side of engineering. It's
easy to overlook how much brain work is required to design the right
tools for creating precision and high tech products.
As part of this emphasis, I took graduate courses in Manufacturing
Machine Design, and Operations for Manufacturing Management. The later
course was my favorite, focusing on the dynamics of variation, Just in Time, throughput, work
in progress, cycle time, etc, in all aspects of the operation.
We built mathematical models of several manufacturing systems,
including this final project
where we optimized the design for a manufacturing operation. As a whole
system it looks pretty complex, but like all complex systems, it
becomes simple when taken one part at a time.
|
Return
to Top |
|
|